Peristaltic Hose Squeeze Pump for TBM
A Peristaltic Hose Squeeze Pump for Tunnel Boring Machines (TBMs) is a specialized piece of equipment designed to handle the demanding and often abrasive slurry conditions encountered in tunneling operations. TBMs are massive machines used for boring tunnels through various types of ground, including soil, sand, and rock. The peristaltic pump plays a critical role in these machines by managing the slurry produced during excavation, which can be highly abrasive and contain solid particles of varying sizes. A Peristaltic Hose Squeeze Pump for TBMs offers a robust, reliable, and efficient method for handling the challenging slurries and fluids encountered in tunneling operations. Its design minimizes wear, prevents leaks, allows for accurate metering, and can handle abrasive and chemically aggressive materials, making it an indispensable tool in modern tunnel construction. By carefully selecting the right pump based on application-specific needs, users can ensure optimal performance and longevity in their operations, contributing to successful tunneling projects.
Peristaltic Hose Squeeze Pump for TBM Applications
– Slurry Management: Essential for removing excavated material from the tunnel face in slurry shield TBMs, where water or bentonite slurry is used to support the tunnel face and transport spoil.
– Grouting Operations: Used for injecting grout behind the tunnel lining to fill voids, stabilize the surrounding ground, and control groundwater.
– Foam Injection: For stabilizing soft ground ahead of the TBM cutterhead, improving cutting efficiency and supporting the tunnel face.
– Additive Delivery: Accurately dosing chemical additives that enhance the properties of the slurry or grout, such as thickeners, defoamers, or accelerators.
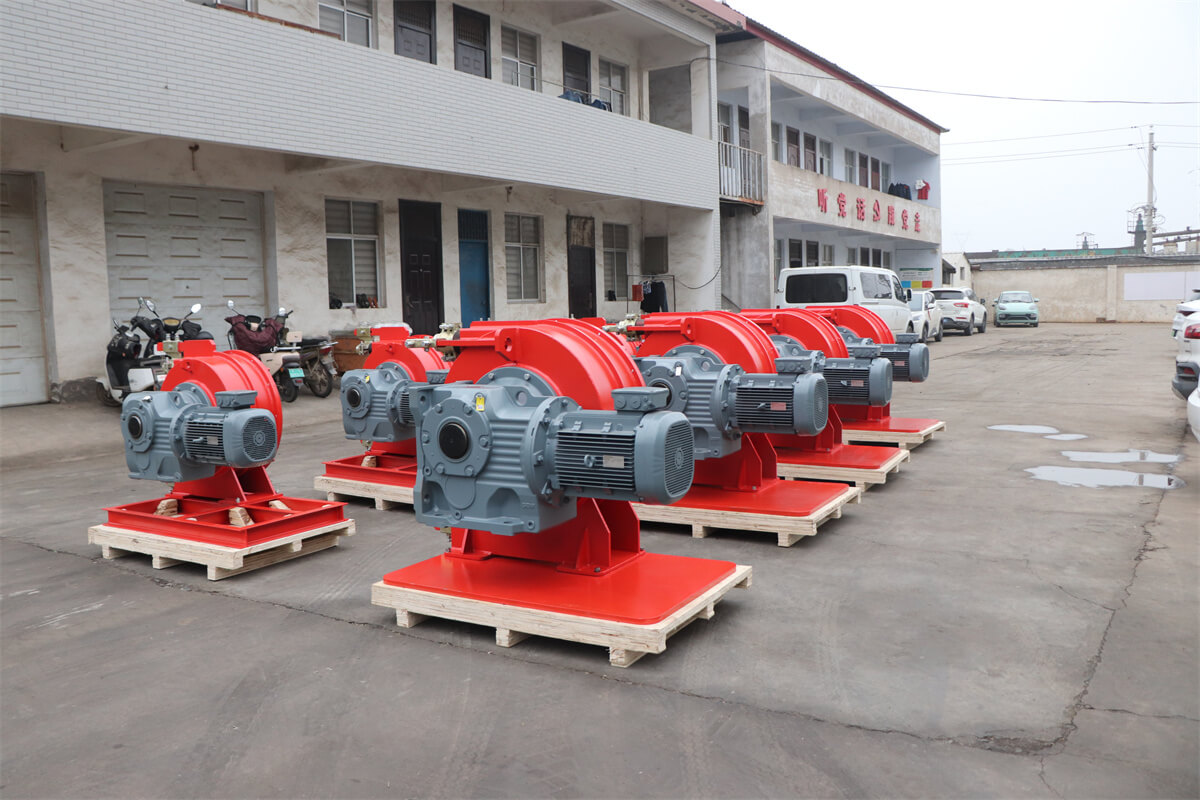
Key Features of Peristaltic Hose Squeeze Pump for TBM:
1. Peristaltic Mechanism:
– Utilizes a flexible hose that is compressed by rollers or shoes moving along its length to move the slurry forward. This design ensures only the inside of the hose contacts the material, minimizing contamination risks and wear on mechanical components.
2. High Abrasion Resistance:
– Hoses are made from specialized materials that can withstand the highly abrasive nature of TBM slurry, which often includes sharp rock fragments and other particulates.
3. Seal-less Design:
– Eliminates the risk of leaks or contamination since there are no seals or valves that come into direct contact with the slurry, reducing maintenance needs and downtime.
4. Self-Priming and Dry Running Capability:
– Can start pumping immediately without being primed and can run dry without damage, providing operational flexibility especially important in variable flow conditions typical of tunneling.
5. Accurate Metering:
– Provides precise control over flow rates, making them suitable for applications where controlled delivery of fluids or slurries is required, such as in slurry management or grouting operations.
6. Gentle Handling:
– Ensures minimal degradation of shear-sensitive components of the slurry, preserving its integrity during transfer. This is particularly important when handling sensitive additives used in tunneling processes.
7. Variable Flow Rates:
– Offers adjustable flow rates to accommodate different project requirements, from low-volume transfers to high-throughput operations, adapting to the changing demands of the tunneling process.
8. Durable Construction:
– Built to handle continuous operation in demanding environments, ensuring long-term reliability even under the harsh conditions of underground construction.
9. Chemical Resistance:
– Hoses are available in various materials (e.g., EPDM, NBR, Viton, PTFE) to handle different types of chemicals and corrosive substances found in TBM slurry.
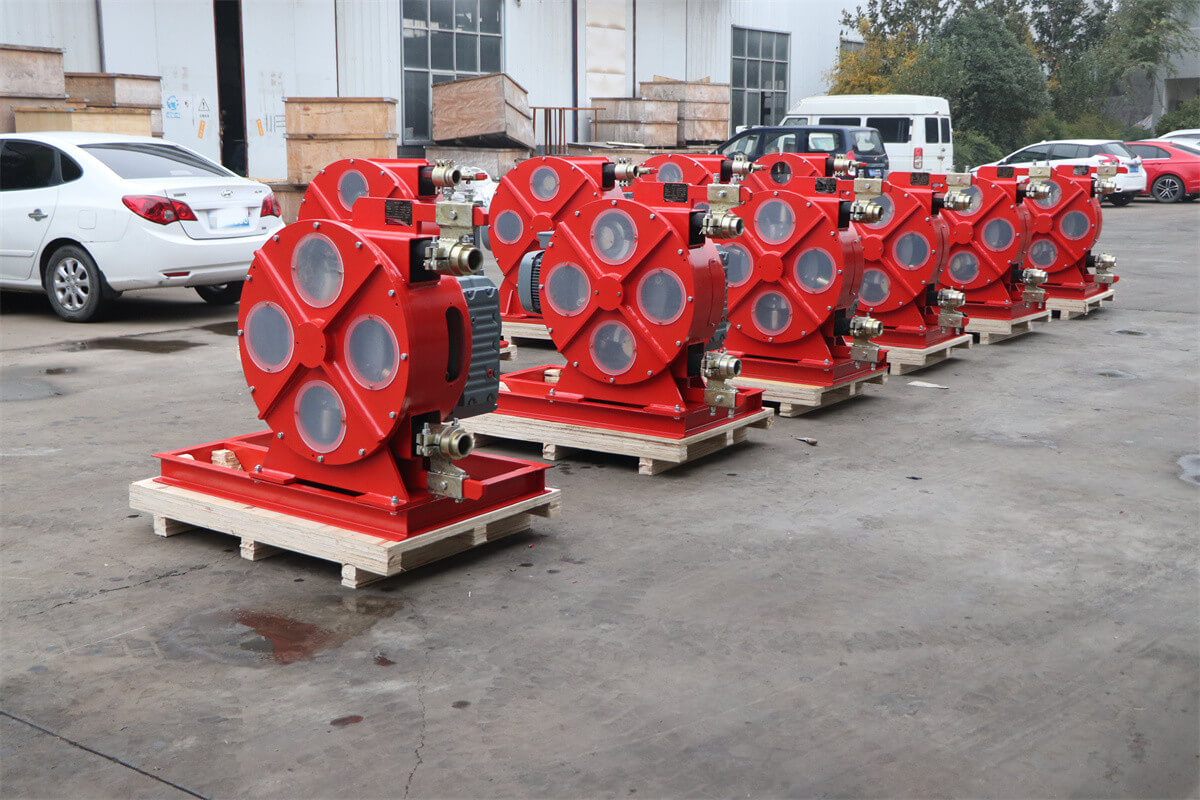
Benefits of Peristaltic Hose Squeeze Pump for TBM:
– Durability: High resistance to abrasion and chemical attack ensures long service life, reducing the need for frequent replacements.
– Low Maintenance: Fewer moving parts reduce maintenance requirements and associated costs, contributing to higher operational uptime.
– Versatility: Capable of handling a wide range of fluid consistencies, from thin liquids to thick slurries, making it adaptable to various tunneling conditions.
– Reliability: Consistent performance even in tough environments and with difficult-to-handle materials, crucial for uninterrupted tunneling operations.
– Safety: Reduced risk of mechanical failures and safer operation due to fewer moving parts exposed to operators.
– Minimal Contamination Risk: The seal-less design minimizes the risk of spills and environmental contamination, important for maintaining site safety and compliance with regulations.
s environmental conditions (temperature, humidity, etc.) under which the pump will operate to select a model that can withstand these conditions.
– Budget and Longevity: Balance initial cost against expected longevity and maintenance costs to find the most cost-effective solution. Consider total cost of ownership, including energy consumption and spare parts availability.
– Automation and Control: Evaluate the need for advanced control systems or integration with existing automation infrastructure, especially for applications requiring precise dosing or remote monitoring.
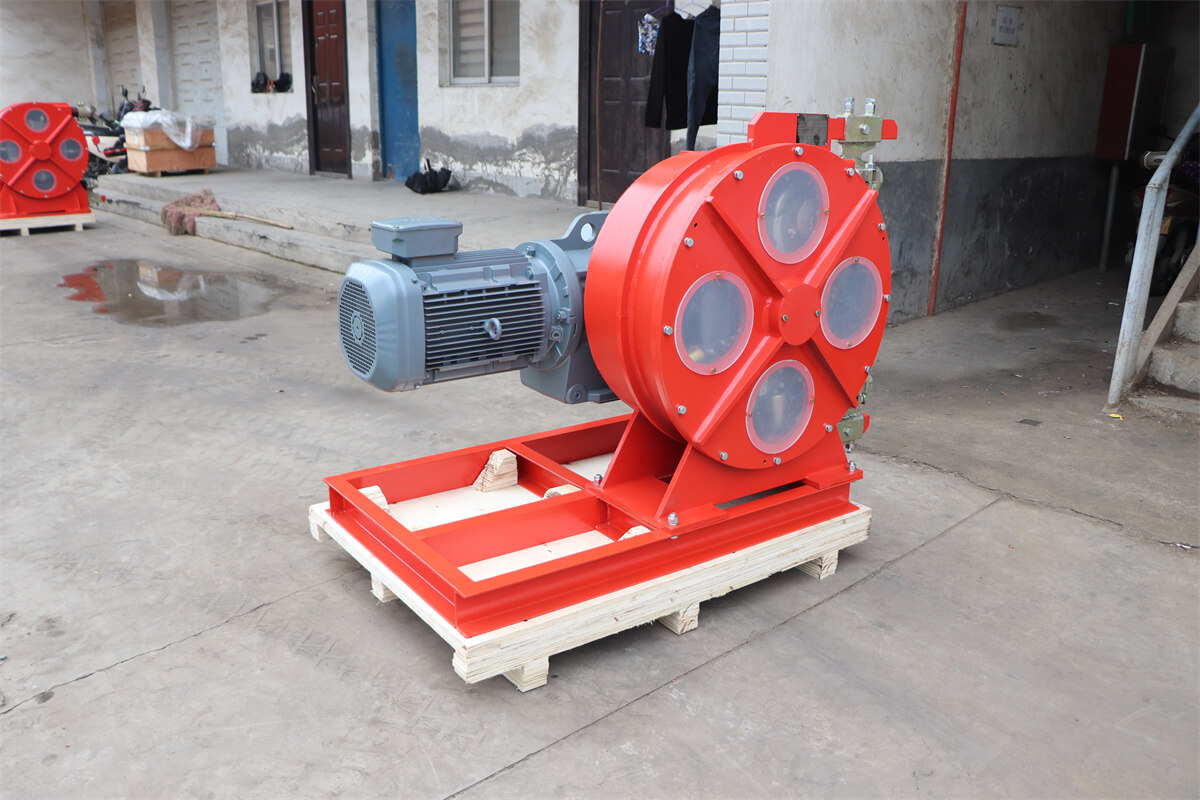