High efficient planetary concrete mixer for float glass mixing ceramic
High-efficient planetary concrete mixer for float glass mixing ceramic has multi-directional movement, the material forms an intersection point, and there is no dead angle. The planetary concrete mixer is especially suitable for difficult mixing, and can quickly mix various material forms to microscopic uniformity.
Planetary concrete mixer for float glass mixing ceramic includes the main rotary shaft, mixing shovel, and side scraper. The mixer adopts advanced mechanical technology from the mixing system, and transmission system to unloading system – single motor design, integrated two-way Planetary reduction mechanism, the connection method of hydraulic coupling, hydraulic unloading method, etc.
High-efficient planetary concrete mixer applicable to industries
1. Building materials: various high-performance concrete, aggregate, fly ash, sludge, mortar, white mud, rock wool, cinder, shale, clay, etc.;
2. Refractory materials: various refractory materials, ramming materials, castable materials, thermal insulation refractory materials, ceramics, etc.;
3. Chemical industry, light industry, metallurgy, casting: ceramic slurry, various precious metal powders, ceramic pigments, carbon, molding sand, water glass, sintering, welding materials; manganese slag, solid waste treatment;
4. Cement prefabricated parts: PC components, comprehensive pipe gallery, RPC cover plate, box culvert, pipe pile, sleeper, permeable brick, autoclaved brick, etc.
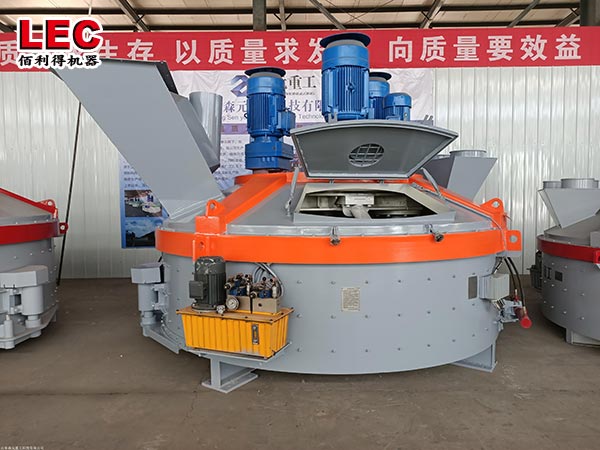
In order to efficiently use and operate the highly efficient planetary concrete mixer for float glass mixing ceramic, avoid mechanical damage, and ensure the normal use of the equipment and the smooth development of the production process, it is recommended that you observe the following contents.
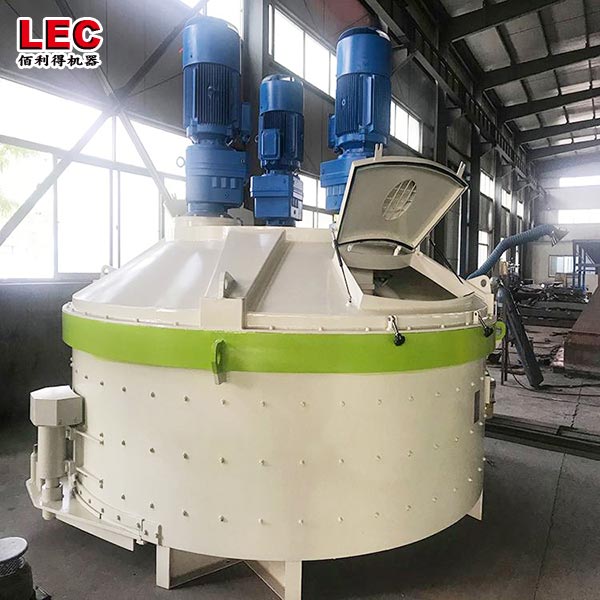
High-efficient planetary concrete mixer for float glass mixing ceramic operation precautions
Inspection content of the vertical shaft planetary concrete mixer before the operation.
The power supply voltage and other adapter instruments have a reasonable rise and fall range, and the relevant installation should be guaranteed to be correct.
The fastening of each transmission system, drive system, and other devices, the layout of the feeding system and gears are complete, and the safety measures are in place.
The wiring of relevant equipment is correct and will not cause safety hazards.
Before the operation of the planetary concrete mixer, conduct an idling test machine to confirm that there is no abnormality.
During the operation of the planetary concrete mixer, it is necessary to pay attention to the abnormal situation and the overheating of some components. If the problem occurs, it should be stopped for inspection and repaired until it is normal.
The wearing parts of the vertical shaft planetary mixer should be replaced in time, and the equipment should be adjusted in time to return to its normal state.
During the use of the vertical shaft planetary mixer equipment, it is necessary to ensure that the operator can operate the equipment, and it is strictly forbidden to leave the work position during operation.
After the completion of each shift of the vertical shaft planetary mixer, it must be cleaned and cleaned in time, the equipment should be lubricated, and the power supply should be cut off.
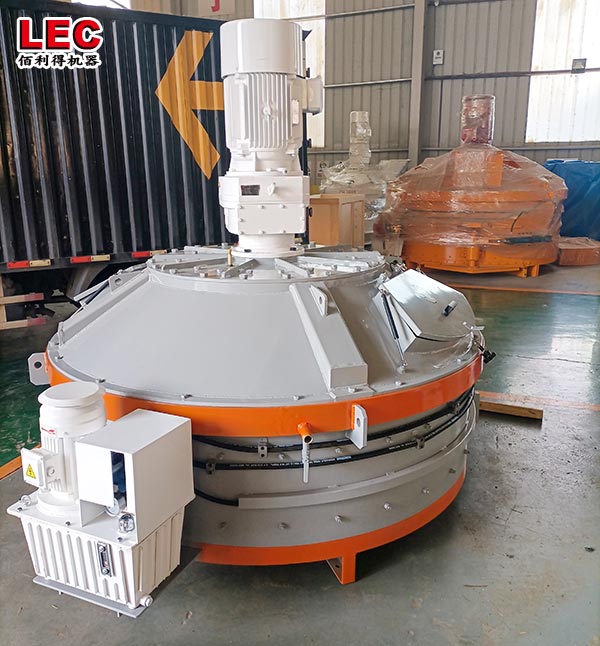
High-efficient planetary concrete mixer for float glass mixing ceramics’ maintenance per shift (before, during, and after each shift)
①Remove the scale and obstacles on the machine body and mixing blade, and check and tighten the bolts of each part. Replace severely worn bolts and nuts.
② Check the position of the lubricating oil of the reducer on the transparent glass window, and the oil level should not be lower than 1/3 of the glass height. (See Figure 2) When the oil level is insufficient, it should be replenished in time.
③ Conduct a test run before the shift to confirm that all mechanisms work reliably, there is no abnormal phenomenon, and the sound is normal. The operating shafts of the discharge door (see 7. Machine lubrication table sequence 2, 3, 5) should be properly refueled.
④Clean the mixer thoroughly after each shift, put water and stones into the mixing drum, run for 10 to 15 minutes, and then clean it with a broom.
