Counter-current planetary concrete mixer for refractory materials
Counter-current planetary concrete mixer for refractory materials is specially made for the production of refractory materials, and can better meet the requirements in terms of mixing uniformity and material fineness. Counter-current planetary concrete mixer for refractory materials features: wear resistance, The wear resistance of the ceramic lining is 271.5 times higher than that of manganese steel; impact resistance, the lining plate, and the mixing blade are not easy to break, and there is a unique buffer layer, which can resist the impact of large materials; high-temperature resistance; acid and alkali resistance; anti-shedding, more tightly combined insurance.
High-quality bauxite and lime are used as raw materials, mixed according to a certain proportion to form raw materials, and the clinker after sintering is ground into fine powder to form a hydraulic cementitious material with fire resistance. This material is called refractory cement.
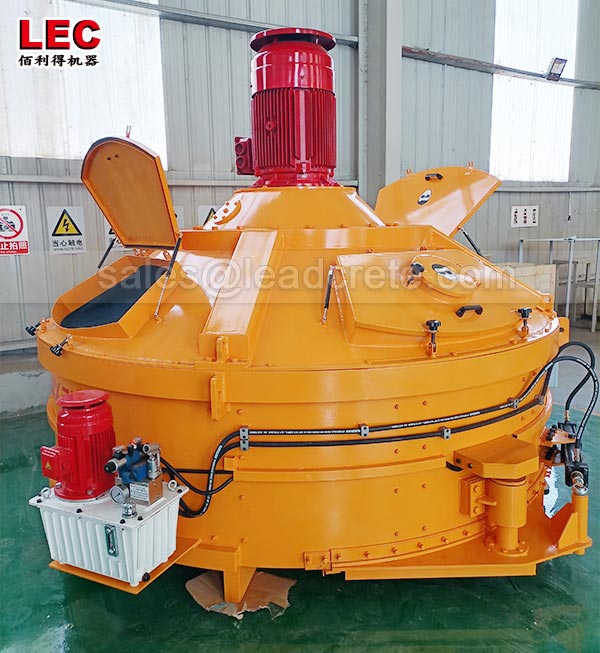
The refractoriness of refractory cement is not lower than 1580 degrees Celsius. There are certain requirements for refractory cement. The finer the particle size of refractory cement, the larger the specific surface area, the faster and more fully the hydration reaction, and the higher the strength. Advanced mixers fail to meet national regulations in terms of mixing fineness, and produce unqualified products.
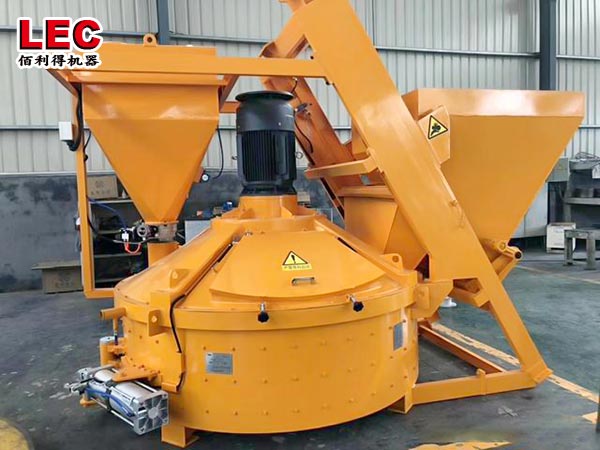
The components of the counter-current planetary concrete mixer for refractory materials are easy to install and replace, reducing the number of after-sales services, reducing the frequency of maintenance, saving cost and labor, and the gearbox is individually designed according to high-strength working conditions, high strength, and high performance. The reducer is self-developed with a longer service life. In the planetary mixing structure, the mixing method of rotation and revolution is more sufficient, and the overall energy consumption is also lower. The mixing tool set can meet the uniform mixing of different materials. The built-in spiral solid nozzle, conical Designed to improve spray uniformity and area coverage.
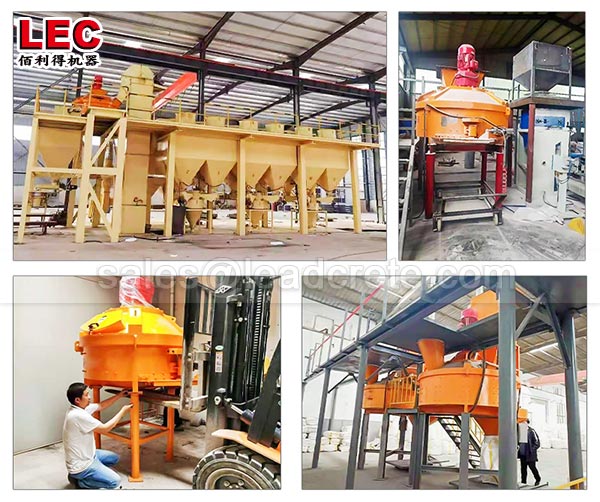