Steel plant equipment - industrial tundish spraying machine for sale
2025-01-21 16:59:49
Tundish spraying machine for mixing and spraying device is a mixing and spraying combined equipment used to process large bags of pre-mixed dry materials for tundish spraying. Through a hopper that can hold about 1.5 tons of dry materials, the dry materials are fed into a continuous mixer, where mixing water is continuously added to process uniform spraying and transported to the mortar pump below. The wet mortar probe adjusts the liquid level of the mortar hopper by automatically switching the continuous mixer. The screw pump transports the spraying mortar to the processing site through a pressure-resistant hose, where it is manually sprayed with a spray gun.
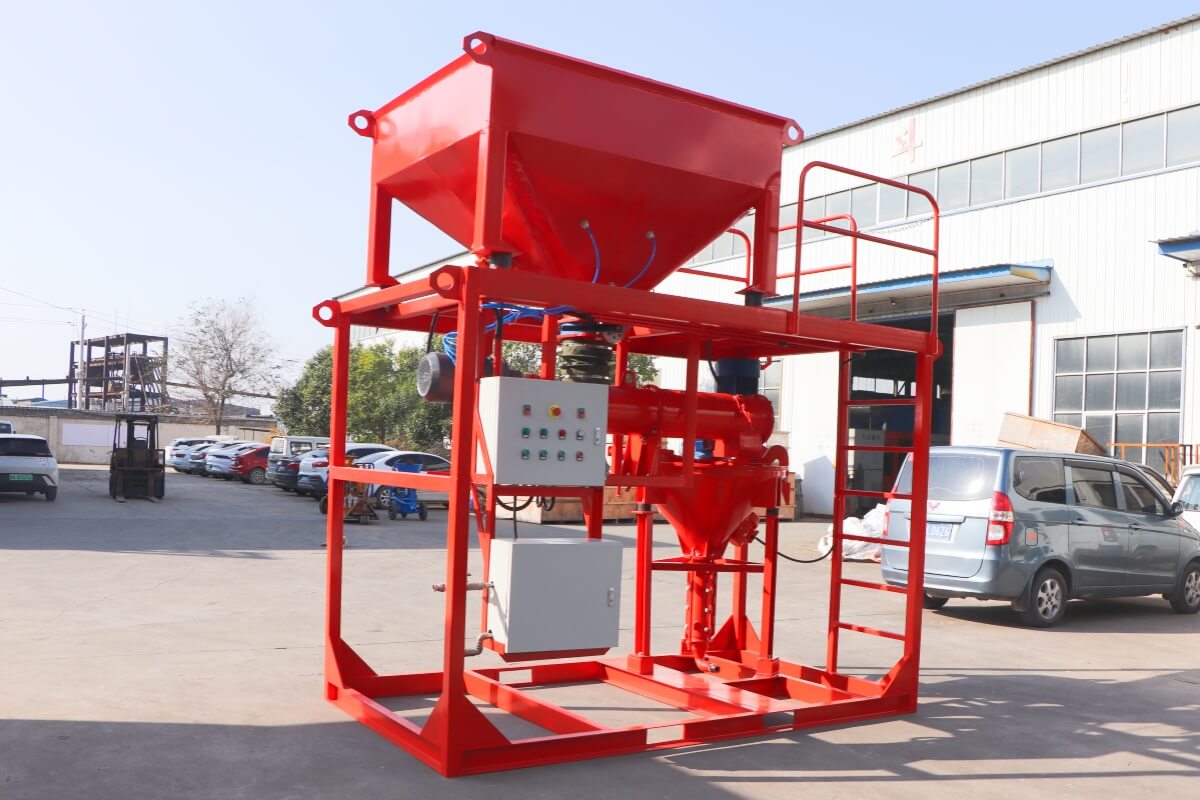
The tundish is a refractory container that first receives the molten steel poured from the ladle and then distributes it to each crystallizer through the tundish water outlet. Its functions are:
(1) reduce the static pressure of the molten steel, maintain a stable molten steel level in the tundish, and inject the molten steel into the crystallizer in a balanced manner;
(2) promote the further floating of inclusions in the molten steel to purify the molten steel;
(3) divert the molten steel. For multi-stream continuous casting machines, the molten steel is distributed to each crystallizer through the tundish:
(4) store the molten steel. When the ladle is replaced during multi-furnace continuous casting, the casting speed is not reduced, creating conditions for multi-furnace continuous casting.
It can be seen that the main functions of the tundish are to reduce pressure, stabilize flow, remove inclusions, store and divert molten steel.
What is the meaning of "tundish metallurgy"?
With the increasing requirements for steel quality, various ladle refining technologies have been developed, the purpose of which is to improve the purity and purify the molten steel "cleaner". The tundish is a refractory container between the continuous casting ladle and the crystallizer. The molten steel after refining outside the furnace can be said to be "clean", but it may be contaminated again when poured into the tundish. Therefore, the tundish should not be regarded as a simple molten steel transition container, but as a continuous metallurgical reactor. The measures adopted in ladle refining can be transplanted to the tundish to further purify the molten steel. For this reason, the concept of tundish metallurgy was proposed and has received attention.
The functions of tundish metallurgy are:
(1) Purification function
In order to produce high-purity steel, measures such as retaining walls and dams, argon blowing, and ceramic filters are used in the tundish to significantly reduce the content of non-metallic inclusions in the steel, and significant effects have been achieved in production.
(2) Temperature control function
In order to make the temperature difference of the molten steel in the front, middle and late stages of the tundish less than 5°C during the pouring process, close to the liquidus temperature, expand the equiaxed crystal zone of the ingot, and reduce center segregation, small pieces of scrap steel can be added to the tundish, iron powder can be sprayed, etc. to adjust the temperature of the molten steel.
(3) Fine-tuning of composition
Aluminum, titanium, boron, etc. are fed into the crystallizer through the center hole of the tundish plug rod to achieve fine-tuning of the micro-alloy composition in the steel, which not only improves the recovery rate of easily oxidized elements, but also avoids nozzle blockage.
(4) Refining function
Double-layer slag is added to the surface of the molten steel in the tundish to absorb the floating inclusions in the steel, or calcium wire is fed into the tundish to change the shape of AI2O3 inclusions and prevent nozzle blockage.
(5) Heating function
Induction heating and plasma heating are used in the tundish to accurately control the pouring temperature of molten steel within ±3~±5℃.
What is the definition and significance of the residence time of molten steel in the tundish?
The time that molten steel spends in the tundish from the time the ladle flows into the tundish to the time it flows into the crystallizer is called the residence time.
Its definition is: t=v/Q
Where
t—residence time of molten steel in the tundish, min;
V—volume of molten steel in the tundish or weight of molten steel, m3 or t;
Q—flow rate of molten steel in the tundish, t/min.
If the weight of the molten steel in the tundish is 18t, the billet is 150×150mm2, and the casting speed v is
2.6m/min, then the molten steel flow Q:
Q= 0.15×0.15×2.6×7.0×4 = 1.638t/min
So t=18/1.638≈11min
That is to say, the molten steel stays in the tundish for 11min. If the molten steel in the tundish flows quickly from the water inlet to the crystallizer, the inclusions will not have time to float up.
The general principle is: the longer the molten steel stays in the tundish, the more time the inclusions have to float up, and the cleaner the molten steel. To increase the residence time of the molten steel, an effective way is to use a tundish with a large capacity and a deep melting pool.
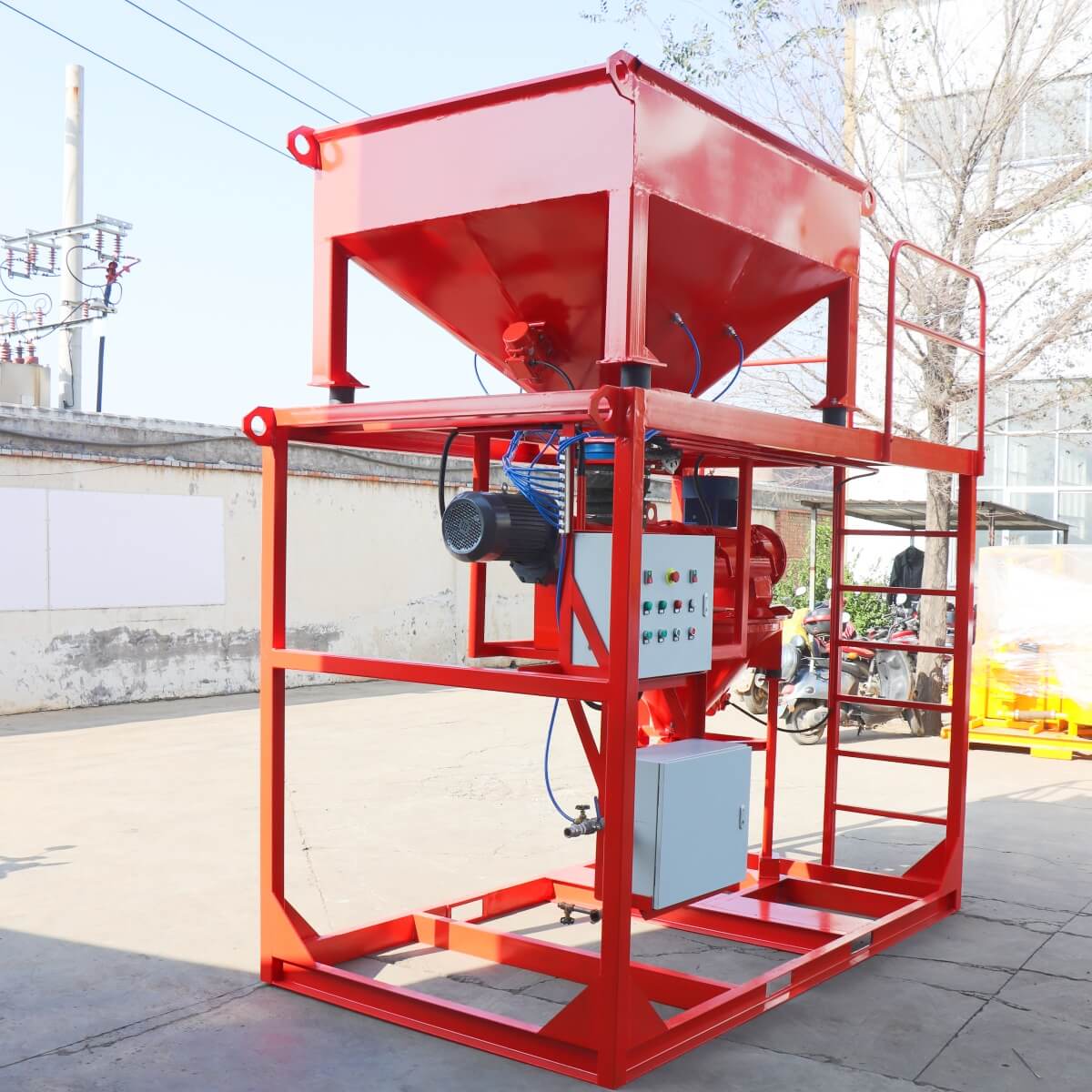
What is the purpose of adding retaining walls and dams to the tundish?
The residence time of molten steel calculated from the capacity of the tundish and the amount of molten steel in the tundish is called the theoretical residence time. However, in actual production, the flow of molten steel in the tundish is uneven, fast in some places and slow in others. In particular, there is an inactive stagnation zone of molten steel at the bottom of the tundish, making it difficult for inclusions to float up. The actual average residence time of molten steel in the tundish is shorter than the theoretical average residence time. In order to fully and effectively utilize the volume of the tundish and promote the floating of inclusions, the measures taken are to add retaining walls and dams to the tundish, the purpose of which is:
- Eliminate the dead zone at the bottom of the tundish.
- Improve the trajectory of molten steel flow, make the flow flow along the steel-slag interface, shorten the floating distance of inclusions, and facilitate slag absorption.
The function of the retaining wall can also limit the strong eddy current caused by the impact of the ladle injection to a local area, and prevent the turbulent diffusion from causing surface fluctuations to roll the slag into the molten steel.
The position and size of the retaining wall and dam should be determined by water model tests in combination with the actual tundish, and then applied in production. After the retaining wall was used in the 10t tundish of the 3# and 4# continuous casting machines of a certain steel plant, the inclusions in the tundish molten steel were reduced by about 30% and the inclusions in the ingot were reduced by 30-40% under the condition that other process conditions remained unchanged. Some experiments pointed out that the use of retaining walls and dams in the tundish improved the cleanliness level of the steel. The aluminate inclusions on the surface of the slab without retaining walls were 2.9%, and with retaining walls, it was 2.1%. With retaining walls and dams, the inclusions on the surface of the slab were reduced from 2.1% to 0.3%.
What is the critical liquid level height of the tundish molten steel?
From life experience, we know that after a container is filled with water, the water flows out from the bottom hole. When the liquid level drops to a certain height, a vortex is generated above the water outlet. This phenomenon also exists in the tundish.
There are two situations for the critical height:
One is how high the molten steel in the tundish is filled before pouring, and pouring begins;
The other is how high the molten steel level drops at the end of pouring to stop pouring.
Both have a critical height. If it is lower than the critical height, the molten steel surface will generate a vortex that will roll the slag into the crystallizer, increasing the inclusions in the steel and causing the product to be scrapped.
When the tundish liquid level reaches a critical height, the pouring will stop, and the tundish will have residual steel loss, which will reduce the molten steel yield.
For example, after 4 furnaces of continuous pouring of a 40t tundish, 10t of molten steel is left, and the yield loss is 0.86%; 12.5t of molten steel is left, and the yield loss is 1.08%. The best choice is to increase the number of continuous pouring furnaces, pour to the lowest liquid level to achieve the best yield, and obtain good billet quality without rolling slag.
The conflict between the loss of molten steel yield and the quality of the billet is mainly determined by the product quality. If the product quality has strict requirements on inclusions, it is better to lose some molten steel; if the quality requirements are not so strict, the critical liquid level height will not be so harsh.
The critical liquid level height can be determined by water model test observation. Depending on the capacity of the tundish, the critical height of the steel liquid level is generally 200-300mm.
What are the characteristics of the flow of molten steel in the tundish?
The flow velocity, flow trajectory and turbulence intensity are generally used to describe the flow characteristics of the fluid.
Flow characteristics of the tundish:
(1) The ladle injection is equivalent to the role of a "jet pump", which draws the surrounding air into the molten steel in the tundish and breaks it into small bubbles, forming additional circulation, aggravating the secondary oxidation of the molten steel.
(2) The impact zone of the ladle injection into the tundish is a highly turbulent area, which is easy to cause slag entanglement.
(3) Vortex formation. At the end of pouring, when the tundish liquid level drops to the critical height, a vortex is formed above the water inlet, which draws the slag into the crystallizer. At the same time, the tundish injection is unstable, stirring the flow of molten steel in the crystallizer.
(4) Surface wave formation. When the tundish steel liquid level is unstable during pouring, ladle replacement and the end of pouring, surface waves are easily generated, causing slag to be drawn into the molten steel.
Therefore, the unstable state caused by the flow of molten steel in the tundish will aggravate the secondary oxidation;
The slag will be drawn into the molten steel, which seriously affects the cleanliness of the steel. Therefore, efforts should be made to reduce the harm caused by the flow, and the following measures should be adopted:
(1) Use a tundish with a large capacity and deep melting pool.
(2) Use a long nozzle from ladle to tundish, which can not only protect the steel flow from secondary oxidation, but also reduce the turbulence in the impact zone of the steel flow and prevent slag rolling.
(3) Set up retaining walls and dams to control the flow trajectory and prevent the diffusion of turbulence in the impact zone.
(4) When changing ladles in continuous casting, efforts should be made to prevent the liquid level from fluctuating too much.
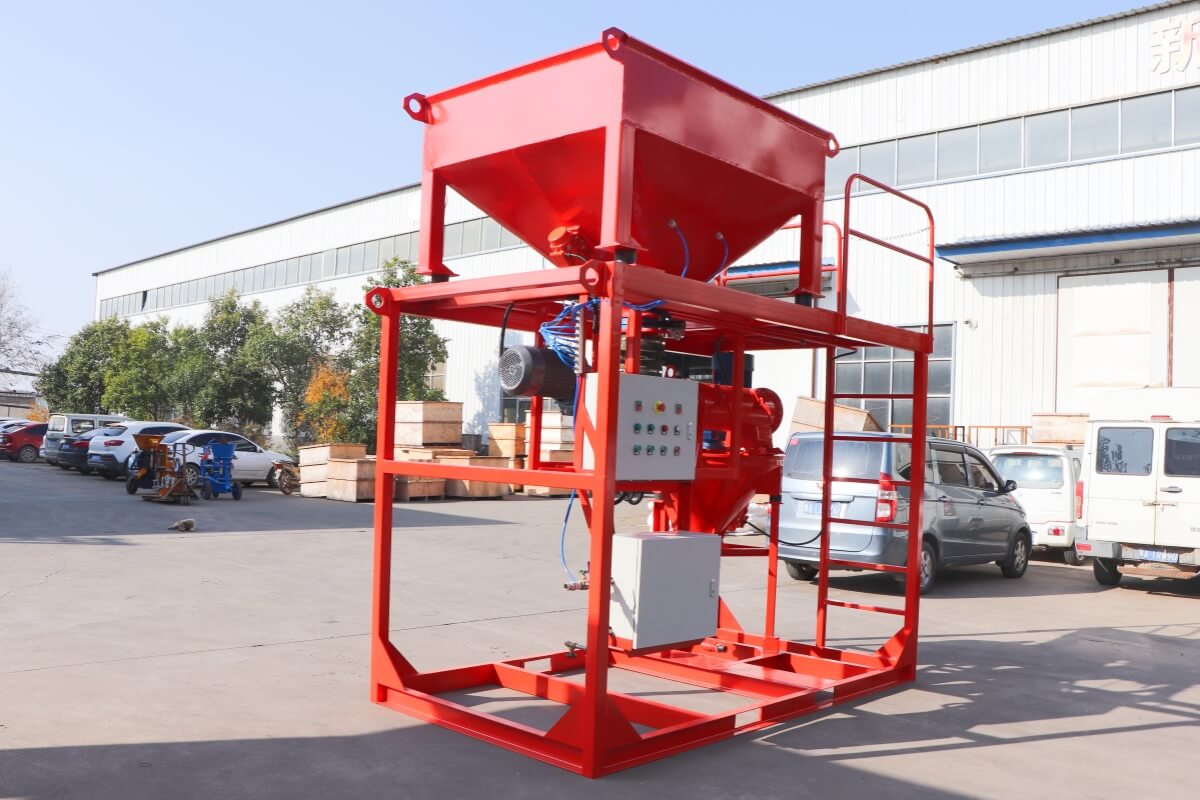
What are the effects of open pouring and long nozzle pouring on the flow of molten steel in the tundish?
The tundish maintains a normal liquid level, and the ladle injection is open pouring. The characteristics of the molten steel flow in the tundish are:
1) The turbulence in the injection impact zone causes wave motion on the surface of the molten steel, which is easy to cause slag rolling.
2) There is shear force along the slag interface, which rolls the slag into the interior.
3) The shear force of the slag interface flow is reduced. 4) Reduces turbulence and wave motion caused by injection.
If the tundish is used in combination with retaining walls and dams, slag entrainment is significantly reduced.
Regardless of the tundish structure, the flow that causes slag entrainment in the tundish is: turbulence in the injection impact zone, surface waves and vortex flow at the slag interface. Therefore, the use of long nozzle casting, deep melting pool tundish, retaining walls and dams are effective measures to prevent slag entrainment.
What is the role of the tundish covering agent?
The functions of the tundish covering agent are:
1) Insulation and heat preservation to prevent heat dissipation;
2) Absorb floating inclusions (such as AI2O3, calcium aluminate);
3) Isolate the air to prevent oxygen in the air from entering the molten steel and prevent secondary oxidation.
However, for steel grades with strict product quality requirements, the content of non-metallic inclusions in the steel must be reduced, especially Al2O3 inclusions, to prevent defects such as cracks and black lines in the product. For this purpose, the tundish lining uses alkaline refractory materials (magnesium insulation board or magnesium coating), and the tundish uses double-layer covering slag, that is, the molten protective slag on the molten steel surface plays the role of absorbing inclusions such as AI2O3, and the rice husk ash is added to play the role of insulation and heat preservation.
The composition of the tundish protective slag is different from that of the crystallizer protective slag. Because the tundish lining is alkaline, in order to prevent the lining from eroding too quickly, the protective slag must have a higher alkalinity and good ability to absorb inclusions.
The above are some descriptions and questions about the tundish. If you need to buy a
tundish spraying machine for steel plant to improve the service life of the tundish and the quality of molten steel, you can contact us - Leadcrete Equipment professional manufacturers and suppliers, and can provide you with the final quality and price. Email address:
sales@leadcrete.com