Air mode gunning & short creting machine for installation at sites in steel plants
2023-01-10 16:13:38
We are an air mode gunning & short creting machines manufacturer, supplier and exporter, with more than 20 years of experience in manufacturing, our refractory gunning & short creting machines have been exported to many countries, such as: United States, Mexico, Canada Serbia, Russia, Philippines, Indonesia, Vietnam, Malaysia, Thailand, Colombia, Egypt, United Arab Emirates, Saudi Arabia, Qatar, Kuwait and other countries.
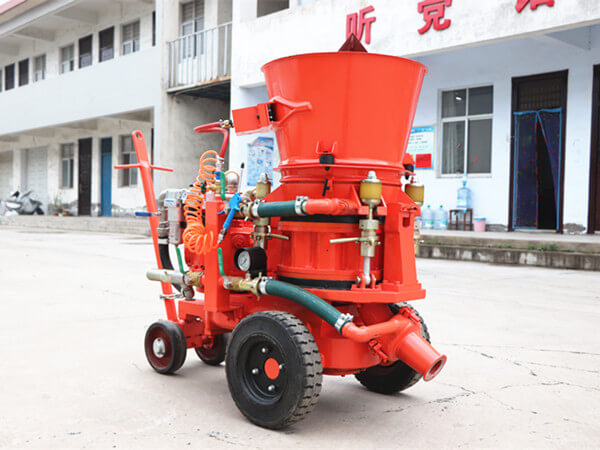
Refractory gunning & short creting machine can be divided into air mode and electric mode according to the driving mode. According to the type of gunning, it can be divided into dry spraying and wet spraying. The displacement of refractory gunning & short creting machine we provide includes 1.5m3/h, 3m3/h, 5m3/h and so on. At the same time, we can also provide you with customized refractory gunning & short creting machine, the scope of customization is: Output Capacity, Voltage and Drive Type.
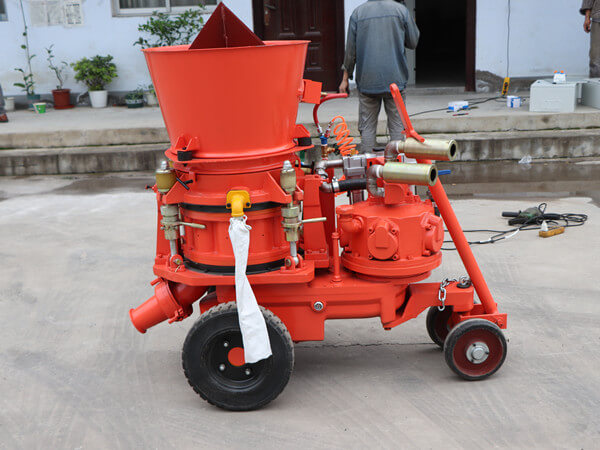
If you need to buy a refractory gunning & short creting machine, specially designed for spraying refractory materials, castable in refractory installing project. Please choose a famous and reliable refractory gunning & short creting machine manufacturer, supplier from China-Leadcrete Equipment. You can contact us to get quotes, information, videos, etc. through website messages, customer service chat or email us directly. Email address: sales@leadcrete.com
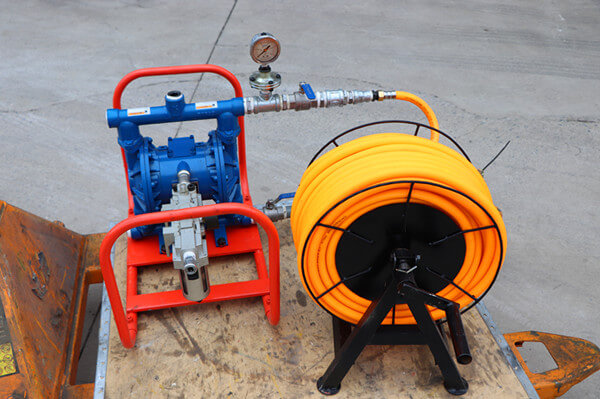
The construction classification of refractory gunning materials for ladles, key technologies of gunning construction, gunning adhesion process of gunning construction, factors affecting adhesion of gunning construction, damage factors of gunning materials in gunning construction, etc. are shared with you. These are steel The factory site workers summed up after years of construction experience.
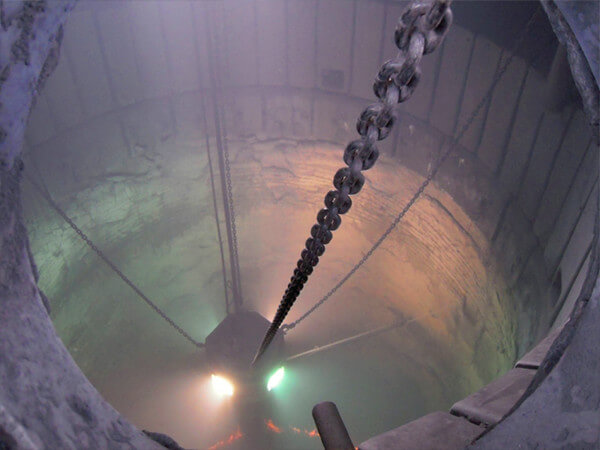
The refractory gunning & short creting machine (or gunning material) is sprayed with a spray gun to spray the refractory mixture onto the sprayed surface, that is, the material applied by spraying method is called refractory spray coating. Spraying is carried out by spraying machine or spray gun, which is a new process in furnace building and furnace repairing.
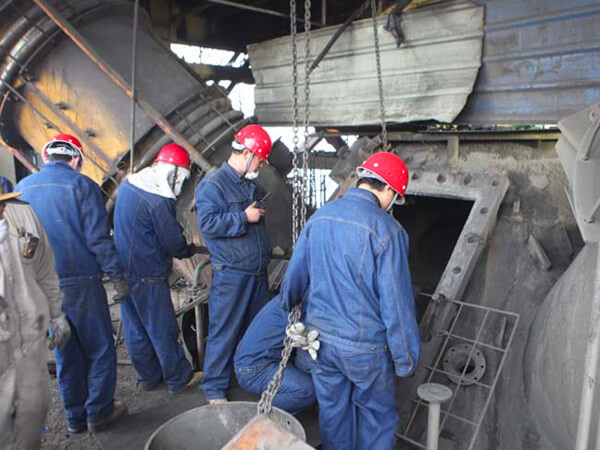
The gunning & short creting machine is compressed air in the silo or pipeline to obtain sufficient speed, and is sprayed on the sprayed surface through the nozzle to form a firm spray coating. Refractory spray coating is an important variety of unshaped refractory materials, and it is a material that has developed rapidly in the past ten years. Its output is only lower than that of refractory castables. On kilns and thermal equipment, this material can be used for spraying new linings, and can also be used for repairing furnace linings. Production practice has proved that this kind of material is an effective technical measure to speed up the construction progress, shorten the furnace repair time, prolong the service life of the kiln and reduce the consumption of refractory materials. .
Ladle gunning construction
1. Classification of gunning construction
It is divided into three types: wet gunning, dry gunning and flame gunning.
Wet gunning
Wet wet spraying refers to the spraying of refractory spray coatings to the sprayed surface after adding water or liquid binder. According to the sequence and amount of adding water (or liquid binder), it is divided into three types: mud method, semi-dry method and pseudo-dry method. Among them, the combination of the two methods is called the mixed method. The mud method is to stir the refractory mixture into mud before spraying, which is mainly used for hot gunning furnace lining; the semi-dry method is to first add a small amount of water to the refractory mixture and stir it evenly, then transport it to the nozzle and add the remaining water After spraying; the pseudo-dry method is to mix the refractory mixture through a mixer, and then transport it to the nozzle to add water and then spray it. The latter two methods are suitable for gunning repair furnace or gunning furnace lining.
Dry gunning
Dry spraying means that the mixed refractory spraying paint is directly sprayed onto the surface to be sprayed through the nozzle, which is mainly used for repairing the furnace.
Flame spraying
Flame spraying is to use oxygen to transport the mixed refractory spray paint to the nozzle to meet with combustible gas and spray it together. The combustible gas burns, and the material travels in the flame and melts into a plastic state and sprays it on the sprayed surface. This method is mainly used for hot spraying furnace lining, which has less damage to the original lining, and the sprayed layer is easy to sinter and has a long service life, but the cost is high.
2. Key technology of gunning construction
During the gunning construction process, the three characteristics that affect the construction quality include adhesion, sintering and erosion resistance.
3. Gunning construction gunning material attachment process
The gunning material is actually composed of a certain proportion of granular material and fine powder. After adding an appropriate amount of water for mixing and stirring, a "dilution system" is formed and sprayed onto the surface of the construction body with high-pressure air as the carrier. The gunning material and the surface of the construction body Contact is divided into initial stage and embedded stage.
Gunning material attachment process
The initial stage includes the wetting and adhesion of the gunning material to the surface of the construction body. At this time, there is no fluid between the gunning material and the construction body, so it is an elastic collision. Only when the fluid reaches a certain thickness and there is fluid extrusion during the impact process The ability to change from elastic impact to plastic impact, but it is difficult to distinguish between the two.
The embedding stage mainly refers to the deformation accumulation of fine powder in the gunning material and the embedding process of particles. If the particle radius of the gunning material is too large, the embedding resistance of the particles will increase, the embedding depth will be insufficient, and the distance between particles will be relatively large, which will have an adverse effect on the use of the gunning material. Usually, the critical particle size is 3 mm.
4. Factors affecting adhesion in gunning construction
Adhesion is the most important performance of the gunning material. Without good adhesion, the gunning material cannot be used. The main factors affecting the adhesion of the gunning material are the particle size composition and rheological properties of the raw material. In addition, curing speed and method (selection of curing agent), ladle lining temperature, water volume and wind pressure, angle and distance between spray gun and ladle lining during gunning operation also play a certain role in the adhesion rate of materials. It can be seen that there are many factors affecting the adhesion rate of gunning material, which is the result of the joint action of many factors.
Granular composition
The particle size composition of the gunning material has a great influence on both adhesion and durability. Fine particle size can improve adhesion performance, good plasticity, and high adhesion rate of gunning material, but large water consumption during gunning will result in low bulk density, high porosity, poor peeling resistance and poor erosion resistance; coarse particles can make spraying The layer is stable, the density of the gunning material is high, and the durability is good. However, when there are too many coarse particles, the spray gun is easy to block, the rebound rate is high, and the loss is large. In severe cases, the gunning efficiency is affected, and the use effect is not ideal. Generally, the proportion of coarse particles in the gunning material should not be too large, and the critical particle size should be about 3 mm, otherwise the rebound rate of the gunning material will increase significantly. Coarse particles are mainly contained in the springback gunning material, which also reduces the performance of the material attached to the ladle lining due to too much fine powder.
Use of binders and curing agents
Under the condition that the particle size composition is determined, the binder and curing agent in the gunning material have a great influence on the adhesion of the gunning material. The binder can ensure the bonding strength of the gunning material during spraying, and the curing agent can thicken and solidify the material in time, maintain a certain fluidity to fill the surface to be sprayed, and have sufficient maintenance strength. However, the amount of curing agent should be moderate. When the amount is too small, the gunning material is wetted when it contacts the surface to be sprayed, but it cannot be set instantly, and the flowing distance of the gunning material is too large, and the adhesion rate is low; , After the gunning material is sprayed out from the nozzle of the spray gun, it will harden and form rapidly at high temperature. When in contact with the lining, it has basically lost its flow characteristics, cannot wet the sprayed surface, and is difficult to adhere to. Generally speaking. The amount of curing agent has a peak value on the adhesion rate, and the suitable range is very small. If the amount of curing agent is not within this range, the adhesion rate of the gunning material will drop significantly.
Water addition and wind pressure selection
During the gunning operation, the selective control of water consumption and air pressure has a great influence on the adhesion. If the amount of water is too small, it will cause "smoking". The gunning material and the surface to be sprayed cannot be wetted due to the small amount of water, and elastic collision occurs, and the material cannot be attached; if the amount of water is too large, the gunning material will flow seriously and cannot be attached. The amount of water used during gunning should be reduced as much as possible under the premise of ensuring the adhesion rate, so as not to affect the performance of the gunning material. During gunning operation, high-pressure air is the carrier for conveying gunning materials. Excessive air pressure will result in insufficient mixing of materials and water at the gun muzzle, unsatisfactory wetting, and excessive elastic collision with the inner lining, resulting in poor adhesion; When it is not enough, the contact between the gunning material and the sprayed surface is insufficient, and the adhesion rate is not ideal.
5. Damage factors of gunning materials in gunning construction
The remaining area of the gunning material gradually decreases with the increase of the number of uses, and the main cause of damage is spalling rather than the melting loss that often occurs in refractory materials. When the gunning material is sprayed onto the surface of the inner village of the ladle with a certain pressure of gas as the carrier, due to the difference in impact force between the particles in the gunning material and the matrix part, a point contact is formed with the inner lining of the ladle, and the bonding strength between it and the inner lining It is guaranteed by these touch points. Even if the ladle lining temperature is 800-1000°C during gunning and repairing, and the temperature can reach up to about 1700°C during use, it is difficult to form a firm ceramic bond with this contact method. Only a direct bond is formed to prevent spalling of the gunning compound and increase durability. The above is what we have learned about refractory material spraying equipment for many years. We hope to provide some support for customers and friends to choose and use equipment smoothly. For more information about refractory material wet spraying equipment, please contact our email: sales@leadcrete.com